61 Process Improvement jobs in Malaysia
Manager, Process Improvement
Posted 1 day ago
Job Viewed
Job Description
At DHL, people mean the world to us. That’s why our goal has always been to attract and retain the best talent over the world. We provide challenge and opportunity for personal and professional development. We recognize the difference you bring to our business, and together we share the pride of building the logistics company for the world.
Under the DHL Supply Chain umbrella, one of the business units of DHL, we provide customized logistics and industry solutions in the areas of supply chain management, warehousing, distribution, value added services, and lead logistics provider services for our customers – helping them deliver better results every day.
Responsibilities- Leading the global business intelligence and reporting agenda for the LLP/4PL account.
- Drives standardization, continuous improvement and innovation in the reporting process in order to improve efficiencies, quality and global customer experience.
- Engaging and driving global stakeholders and users on data-driven changes to processes, services, and solutions to improve efficiencies and add value by generating and presenting insights extracted from data analysis.
- Single Point of Contact (SPOC) in creating in depth performance analysis, statistics, trends, reports, benchmark studies, and translate data into meaningful and actionable insights to aid decision making purposes.
- Analyzing data to enable logistics, transportation, freight, compliance, controls, quality trend analysis of volumes, costs, and performance to drive improvements and or corrective actions based on mid-term forecasting and planning time horizon.
- Mediating between IT and the business leveraging data analytics to assess process, determine requirements and deliver data-driven recommendations and reports.
- Owner for Oracle Transportation Management (OTM) system database and master data maintenance. This includes collaborating with global teams to troubleshoot and support resolution.
- Support ad-hoc projects and corresponding data analysis as requested. I.e. Quarterly and Monthly Business Review Meetings, Pre-bid Logistics Service Providers data analysis, Spot Quote Analysis, System (Control Tower, Transportation Management System, PowerBI), scope expansion projects, and etc.)
- Preferably candidate who possess a degree in Supply Chain or Computer Science.
- Minimum 5 years of experience in performing data analysis and continuous improvement (CI) programs in Distribution and Logistics domain.
- Expertise in Microsoft PowerBI and OTM system. Building, publishing customized interactive dashboards and report scheduling.
- Enable drill-down data capability to visualize data in the best possible way through charts, reports, and dashboards.
- Comprehensive knowledge of data design, data modelling, data management, and data visualization.
- Good analytics skills for data and operational processes. Excellent knowledge of Microsoft Excel, PowerPoint, and Visio. Knowledge on ERP (SAP), distribution and logistics processes of supply chain in the manufacturing industry.
- Self-starter with good in expressing area of development. Strong communication, global stakeholder/client management and interpersonal skills, with proven ability to work in a global team setting and foster positive relationships.
PROCESS IMPROVEMENT EXECUTIVE
Posted 1 day ago
Job Viewed
Job Description
Job Details:
Job SummaryWe are looking for a detail-oriented and proactive Inventory Planning Executive to manage raw materials and finished goods inventory. You will ensure stock accuracy, optimize stock movements, coordinate deliveries, and support financial and compliance requirements.
Key Responsibilities- Raw Material & Finished Goods Inventory Management
- Plan, schedule, and arrange raw material replenishment for production needs.
- Ensure adequate stock levels of finished goods to fulfill customer orders.
- Apply the First Expiry, First Out (FEFO) principle in stock issuance.
- Prepare Stock Transfer Orders (STO), Purchase Orders (PO), and outbound documents for deliveries and stock transfers.
- Order Fulfillment & Stock Allocation
- Coordinate with Production Planning, Procurement, Purchasing, Commercial, and Customer Service to ensure smooth order fulfillment.
- Arrange and monitor deliveries from Subang & Enstek Plants or 3PL Warehouses according to customer requirements.
- Provide accurate information for export documentation to support smooth delivery processes.
- Inventory Accuracy & Reconciliation
- Maintain and reconcile inventory records between 3PL Warehouses and Tyson Malaysia plants.
- Conduct monthly stock counts and reconciliations to ensure accurate inventory reporting.
- Monitor weekly storage capacity to prevent overflow and maintain optimal stock levels.
- Stock Aging & Compliance Monitoring
- Track weekly stock aging reports , managing non-moving and near-expiry inventory .
- Ensure QA compliance for all raw materials and finished goods before dispatch.
- Maintain product traceability records to comply with audit and regulatory requirements .
- Financial & Reporting Support
- Assist in weekly, monthly, and annual financial closing activities related to inventory.
- Provide inventory data and reports to support decision-making.
- Additional Responsibilities
- Handle any ad-hoc tasks assigned by the superior to support business needs.
Bachelor's degree in Supply Chain Management, Logistics, Business Administration, or a related field .
2-3 years of experience in inventory planning, warehouse management, or supply chain operations .
Knowledge of WMS, and ERP Systems . Experience in the SAP system is an advantage.
Strong analytical skills with experience in Microsoft Excel for reporting.
Ability to work independently in a fast-paced environment.
Relocation Assistance Eligible: No
Work Shift:
Tyson is an Equal Opportunity/Affirmative Action Employer. All qualified applicants will be considered without regard to race, national origin, color, religion, age, genetics, sex, sexual orientation, gender identity, disability or veteran status.
#J-18808-LjbffrBusiness Process Improvement Engineer
Posted 1 day ago
Job Viewed
Job Description
JOB DESCRIPTION
- Identify, create, and participate in the implementation of business process improvements, enabling tools, and systems
- Perform qualitative and quantitative analysis of key performance indicators to identify opportunities for improvement in the existing business model, processes, and structure.
- Identify subject matter experts to support multi-functional efforts in process improvement, data capture and analysis, and compliance with policies & procedures.
- Analyse and develop business process diagrams and models to support process design and redesign initiatives
- Advisor on projects, offering solution-design support and best practices for process management.
- Ensure on time delivery of the tasks and projects.
- Meeting and exceeding management and peers' expectations on the department services.
- Degree in Engineering (or equivalent)
- BPI certification (Lean, Six Sigma) or experience with Kaizen a plus
- Data Analytics certification a plus
- Power Platform Certification a plus
- Minimum 1 years of business process improvement experience.
- Demonstrate applied knowledge of business process and process improvement methodologies.
- Ability to interface and communicate effectively with all levels of employees, management, and diverse audiences.
- Demonstrated ability to lead complex projects from inception through completion.
- Knowledge of principles and methodologies of change management.
- Strong verbal and written communication skills as BPI to communicate with the wider business stake holders.
Business Performance and Process Improvement Specialist
Posted 1 day ago
Job Viewed
Job Description
Performance Management & Reporting
- Design and implement KPIs that align with evolving business needs.
- Act as a subject matter expert to internal managers, providing data-driven insights.
- Analyze and distribute performance reports via Power BI, Excel, Power Query, and SharePoint.
- Interpret datasets to highlight trends, risks, and opportunities.
- Ensure accuracy and consistency across reporting sources.
- Build dashboards and data models to support decision-making.
- Prepare monthly, quarterly, and annual presentations and reports.
Process & Continuous Improvement
- Lead Lean Six Sigma projects to improve efficiency and quality.
- Facilitate workshops to build a continuous improvement mindset across teams.
- Recommend and implement process automation and enhancements.
- Conduct process mapping and propose strategic improvements.
Service Management
- Ensure service delivery meets SLA/KPIs.
- Support BCP initiatives and issue resolution.
- Use performance data to track project status and highlight root causes.
- Bachelor's degree from an accredited college or university
- Strong background in process standardization, KPI setting, and performance analysis
- Solid understanding of BPO/GBS metrics, reporting, and industry best practices
- Extensive experience with Lean Six Sigma methodologies
- Proven ability to collaborate effectively with cross-functional and regional teams
- High proficiency in Power BI, Microsoft Excel, PowerPoint, and case management tools
- Excellent written and verbal communication skills
- Strong presentation skills with both technical and business acumen
- Experience working with key business units such as:
- Finance (Accounts Payable/Receivable)
- Human Resources (Onboarding, Payroll, Master Data)
- Business Operations
- Comfortable handling manual data processes in environments with limited system support
- Drive Strategic Impact through Data & Improvement Initiatives
- Be at the Heart of Cross-Functional Collaboration Across Business Functions
ROO Training and Process Improvement Officer
Posted 1 day ago
Job Viewed
Job Description
Job Description:
Newcomer Onboarding
The Training and Process Improvement Officer has the key responsibility to onboard all ROO newcomers and ensure they have all the required tools and training to perform their expected task. Trainer’s responsibility includes but is not limited to scheduling and conducting all the training phases for the newcomer including the examination for the new officer to qualify as RO Solver.
Competency Management
The trainer also identifies what are the current team members gaps, proposes and provides refresher training or coordinates with external stakeholders to provide training for team upscaling.
User guide and Process Improvement
Under Process Improvement, they are to coordinate with WHS & ACD Managers, Team Leaders and also other FHS stakeholders (MFT) to ensure that processes are adhered to as per current RO User Guide and work jointly on improvement plans where gaps are identified. The Process Improvement team is then responsible to ensure the deployment of new processes, rules and regulations.
Component Issue Management (CIM)
Other responsibilities of Training and Process Improvement Officer are , but not limited to, being a member of the FHS Component Issue Management (CIM) Forum for ROO related topics and also the monitoring of ROO subcontractor performance.
This job requires an awareness of any potential compliance risks and a commitment to act with integrity, as the foundation for the Company’s success, reputation and sustainable growth.
Company:
Airbus Customer Services Sdn BhdEmployment Type:
Permanent---
Experience Level:
ProfessionalJob Family:
Improvement & Performance ManagementBy submitting your CV or application you are consenting to Airbus using and storing information about you for monitoring purposes relating to your application or future employment. This information will only be used by Airbus.
Airbus is committed to achieving workforce diversity and creating an inclusive working environment. We welcome all applications irrespective of social and cultural background, age, gender, disability, sexual orientation or religious belief.
Airbus is, and always has been, committed to equal opportunities for all. As such, we will never ask for any type of monetary exchange in the frame of a recruitment process. Any impersonation of Airbus to do so should be reported to .
At Airbus, we support you to work, connect and collaborate more easily and flexibly. Wherever possible, we foster flexible working arrangements to stimulate innovative thinking.
#J-18808-LjbffrQuality & Process Improvement Engineer (Teradyne, Penang)
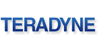
Posted 5 days ago
Job Viewed
Job Description
TERADYNE, where experience meets innovation and driving excellence in every connection. We are fueled by creativity and diversity of thought and in our workforce. Our employees are supported to innovate and learn something new every day.
We cultivate a culture of inclusion for all employees that respects their individual strengths, views, and experiences. We believe that our differences enable us to be a better team - one that makes better decisions, drives innovation and delivers better business results.
Opportunity Overview
The Quality & Process Improvement Engineer is a hybrid role designed to manage the organization's Quality Management System (QMS) while also guide process improvement and digital transformation initiatives. This position will be responsible for ensuring compliance with industry standards, driving continuous improvement projects, and utilizing information technology to optimize business processes. The ideal candidate is a versatile professional who excels in quality management, process engineering, and the use of technology to enhance operational efficiency.
+ Quality Management:
+ Oversee the Quality Management System (QMS), ensuring compliance with relevant standards (e.g., ISO 9001) and regulatory requirements.
+ Conduct internal audits, manage corrective actions, and ensure continuous improvement of quality processes.
+ Develop, implement, and monitor quality policies, procedures, and metrics across the organization.
+ Responsible for root cause and problem-solving activities to address quality issues and customer complaints.
+ Process Improvement & Design:
+ Collaborate with cross-functional teams to identify, prioritize, and implement process improvement initiatives.
+ Facilitate workshops and training sessions to promote a culture of continuous improvement.
+ Design and document efficient business processes, ensuring they align with company objectives and industry's best practices.
+ Develop tools and frameworks for process standardization and optimization.
+ Digital Transformation & IT Integration:
+ Utilize information technology tools to support data examination, process automation, and workflow optimization.
+ To partner with IT and operational teams to design digital solutions that enhance process efficiency and user experience.
+ Leverage data to identify trends, measure process performance, and drive informed decision-making.
+ Stay updated on emerging technologies and industry trends to recommend and implement innovative solutions.
+ Leadership & Collaboration:
+ Serve as a change agent, fostering a culture of quality and continuous improvement across the organization.
+ Responsible for cross-functional project teams to execute complex process improvement initiatives.
+ Provide mentorship and guidance to team members on quality management and process improvement methodologies.
All About You
We seek individuals who share our passion and determination. Our commitment to customer success drives us to go the extra mile. If you're ready to join us in this mission, take a closer look at the minimum criteria for the position.
+ Bachelor's degree in engineering, Business Administration, Information Systems, or a related field.
+ 5+ years of experience in Manufacturing environment, Business Process Engineering, Quality Management or a similar role.
+ Strong knowledge of quality standards (e.g., ISO 9001), process improvement methodologies (e.g., Lean, Six Sigma), and project management.
+ Experience in process design, mapping, and optimization using software tools (e.g., Visio, BPM tools).
+ Proficiency in data analysis and familiarity with IT tools such as ERP systems, data visualization software (e.g., Power BI, Tableau), and automation platforms.
+ Excellent problem-solving, investigation andd decision-making skills.
+ Strong communication and interpersonal skills, with the ability to guide projects and influence stakeholders at all levels.
Additional Requirements:
+ Six Sigma Green Belt or Black Belt certification.
+ Experience with digital transformation projects or IT systems implementation.
+ Familiarity with industry-specific regulations and compliance requirements.
+ May require occasional travel to company locations or client sites.
+ Ability to work in a dynamic environment, manage multiple projects, and adapt to changing priorities.
Benefits:
Teradyne offers a variety of robust health and well-being benefit programs, including medical, dental, vision, fitness and health, heath screening, insurance (Term Life, Personal Accident and Hospitalization and Surgical), time off (annual leave starting with 15 days), tuition assistance programs, and more.
#LI-GQ1
Current openings may involve access to export controlled technology and may be subject to export licensing requirements prior to employment. ATTENTION APPLICANTS WITH DISABILITIES: If you're unable to access our on-line application due to a disability you may visit one of our locations or our Corporate Office at 600 Riverpark Drive, North Reading, MA and request a paper application form. In addition, you may also contact the HR Service Center at or contact them at for additional assistance. LitePoint, a Teradyne Company is an equal opportunity employer and all qualified applicants will receive consideration for employment without regard to race, color, religion, sex, national origin, sexual orientation, age, disability status, protected veteran status, or any other characteristic protected by law. We are a VEVRAA Federal Contractor.
ROO Training and Process Improvement Officer
Posted today
Job Viewed
Job Description
Employment Type: Permanent --- Experience Level: Professional
Job Family: Improvement & Performance Management By submitting your CV or application you are consenting to Airbus using and storing information about you for monitoring purposes relating to your application or future employment. This information will only be used by Airbus. Airbus is committed to achieving workforce diversity and creating an inclusive working environment. We welcome all applications irrespective of social and cultural background, age, gender, disability, sexual orientation or religious belief. Airbus is, and always has been, committed to equal opportunities for all. As such, we will never ask for any type of monetary exchange in the frame of a recruitment process. Any impersonation of Airbus to do so should be reported to
. At Airbus, we support you to work, connect and collaborate more easily and flexibly. Wherever possible, we foster flexible working arrangements to stimulate innovative thinking.
#J-18808-Ljbffr
Be The First To Know
About the latest Process improvement Jobs in Malaysia !
Quality Control Executive
Posted 1 day ago
Job Viewed
Job Description
Join to apply for the Quality Control Executive role at Alpro Pharmacy Sdn Bhd
Join to apply for the Quality Control Executive role at Alpro Pharmacy Sdn Bhd
Alpro Pharmacy Sdn Bhd provided pay rangeThis range is provided by Alpro Pharmacy Sdn Bhd. Your actual pay will be based on your skills and experience — talk with your recruiter to learn more.
Base pay rangeJob Responsibility
- Conduct routine quality control tests on raw materials, in-process samples, and finished milk powder products using approved methodologies and equipment.
- Perform regular inspections of production lines, ensuring adherence to quality standards and taking representative samples for analysis.
- Oversee the calibration and maintenance of quality control equipment to ensure accurate and reliable test results.
- Responsible for in-going and out-going inspection process.
- To monitor all non-conformance products, matter and liaise with related department for corrective action and preventive action.
- Implement quality control policies, procedures, and standards for inspection, assist in updating QC Manual.
- Troubleshoot manufacturing quality issues.
- To involve in performing internal and external audits to determine compliance to Food Safety / HACCP / GMP and identify areas for improvement.
- Record and maintain accurate data related to quality control tests and inspections.
- Analyze the data to identify trends or deviations that require attention.
- Adherence to hygiene and safety protocols in the quality control laboratory and during sampling procedures.
- Responsible for the Food Safety issues.
- Support ad-hoc tasks as and when required.
- A bachelor's degree in Food Science, Food Technology, Chemistry, or a related field is typically required.
- Must fluent in Mandarin as requires dealing with Mandarin speaking internal.
- Fresh graduates are welcome to apply
- Preferably good knowledge in GMP / HACCP / HALAL.
- Prior experience in quality control within the food or dairy industry, knowledge in milk powder manufacturing, is a plus.
- Ability to identify and address quality issues, investigate root causes, and implement corrective actions.
- Familiarity with laboratory equipment and techniques used in quality control testing.
- Career Development
- Medical
- Staff Meal
- Badminton Club
- Seniority level Entry level
- Employment type Full-time
- Job function Other
- Industries Pharmaceutical Manufacturing
Referrals increase your chances of interviewing at Alpro Pharmacy Sdn Bhd by 2x
Get notified about new Quality Control Executive jobs in Seremban, Negri Sembilan, Malaysia .
Quality Control Executive (Foods Products) Mandarin Speaker Mandarin Speaking Quality Control ExecutiveWe’re unlocking community knowledge in a new way. Experts add insights directly into each article, started with the help of AI.
#J-18808-LjbffrExecutive, Quality Control
Posted 1 day ago
Job Viewed
Job Description
We are looking for an Executive, Quality Control who will be a firm advocate of quality in our business, making our customers enjoy our merchandise so that our company can achieve long-term success. Your duties will include verification of all incoming and outgoing material and products as well as inspection of procedures.
You should possess a trained eye for detail, be reliable and committed. In-depth knowledge and excellent comprehension of quality standards are also required.
Your Day to Day- Assist our registered dealer during car collection.
- Verify any dealer complaint technical issue (Engine, transmission problem, mechanical or electrical issue).
- Provide justification on dealer complaints.
- Negotiate and discuss with our dealer regarding car issues.
- Troubleshoot and handle repairs for cars needing repair.
- Conduct last car inspection before handing the car to dealers.
- Automotive background or experience.
- Basic knowledge of Body & Paint; car accident check is an advantage.
- Knowledge about car part prices and labor costs is an advantage.
- Driving license is a mandatory requirement.
- Able to communicate well and follow instructions.
- Able to work on public holidays and weekends.
- Able to relocate within the Klang Valley area.
Quality Control Manager
Posted 1 day ago
Job Viewed
Job Description
Join to apply for the Quality Control Manager role at Kenvue
Join to apply for the Quality Control Manager role at Kenvue
What We Do
Kenvue Is Currently Recruiting For A:
Quality Control Manager
What We Do
At Kenvue, we realize the extraordinary power of everyday care. Built on over a century of heritage and rooted in science, we’re the house of iconic brands - including NEUTROGENA, AVEENO, TYLENOL, LISTERINE, JOHNSON’S and BAND-AID that you already know and love. Science is our passion; care is our talent.
Who We Are
Our global team is ~ 22,000 brilliant people with a workplace culture where every voice matters, and every contribution is appreciated. We are passionate about insights, innovation and committed to delivering the best products to our customers. With expertise and empathy, being a Kenvuer means having the power to impact millions of people every day. We put people first, care fiercely, earn trust with science and solve with courage – and have brilliant opportunities waiting for you! Join us in shaping our future–and yours. For more information, click here.
Role Reports To:
Make Quality Lead - Malaysia
Location:
Asia Pacific, Malaysia, Selangor, Petaling Jaya
Work Location:
Fully Onsite
What You Will Do
Kenvue is currently recruiting for:
Quality Control Manager
This position reports into Make Quality Lead - Malaysia and is based at Petaling Jaya, Malaysia.
Who We Are
At Kenvue , we realize the extraordinary power of everyday care. Built on over a century of heritage and rooted in science, we’re the house of iconic brands - including NEUTROGENA, AVEENO, TYLENOL, LISTERINE, JOHNSON’S and BAND-AID that you already know and love. Science is our passion; care is our talent. Our global team is made by 22,000 diverse and brilliant people, passionate about insights, innovation and committed to deliver the best products to our customers. With expertise and empathy, being a Kenvuer means to have the power to impact life of millions of people every day. We put people first, care fiercely, earn trust with science and solve with courage – and have brilliant opportunities waiting for you! Join us in shaping our future–and yours. For more information, click here.
Role reports to: Make Quality Lead - Malaysia
Kenvue Malaysia Office Address: JNTL (Malaysia) Sdn. Bhd. Lot 3 & 5 Jalan Tandang, 46050 Petaling Jaya, Selangor, Malaysia Malaysia
What You Will Do
The Quality Control Manager is responsible for implementing methods and procedures for inspection, testing and evaluation, mentoring and supervising the quality control staff, evaluating performance and providing opportunities for growth, communicating department objectives and metrics, and initiating audits to verify prompt and appropriate actions:
Part A: Overall Responsibility
- Responsible in providing key direction and oversight to Quality Control Laboratory and ensure the laboratory operation is in accordance with Good Laboratory Practice, Good Manufacturing Practice and Environment, Health & Safety requirement accordingly to Company Quality Policy Standards and applicable Regulatory Requirements.
Quality Control Laboratories
- Overall lead in the implementation of Quality Management System in the lab. To lead and manage the entire Quality Control laboratory operations in accordance to GMP, GLP and Quality System Requirements and driving the lab metrics adherence.
- To support in performing testing and analysis for bulk sample, finished good, raw material and environmental samples and ensure timely results availability.
- To ensure that lab equipment is validated, calibrated, and maintained as per GLP requirements. Accountable for product disposition and compliance decisions of QC programs. Ensures quality data review and timely material and product release
- Ensure appropriate experimental design and test method validated to assure accuracy in results generated to support new product launch.
- Troubleshoots and solves high risk and high complexity issues, using experience, ingenuity, and creativity to implement solutions across a wide range of root causes. Responsible for management of lab investigations.
- Accountable for product disposition and compliance decisions of QC programs. To ensure GLP and data integrity fully adhere by lab analysts.
- Assures compliance with all local government regulatory requirements and requirements related to things such as sampling plans, design control, and quality systems.
- Ensure audit readiness in entire Quality Control Laboratory in both internal and external audits.
- Responsible in the overall management of Quality Control Laboratory housekeeping and safety. Ensure compliance to EHS&S requirements for the lab.
- Provides overview or detailed communications to Q&C and cross-functional leadership on QC Lab performance status of initiatives and issues. This communication occurs at a plant-level, and at a regional-level.
- Build strong interdependent and truly partnership with the local Operation. Support the plant initiatives including resource management for lab activities.
- Organizes, plans, leads, and manages quality related projects in alignment with company goals. Lead the design and implementation of safety, Q&C, customer service and cost improvement programs and initiatives.
- Innovate solutions to significant quality system gaps and lead continuous improvement projects
- Be part of the assessment team for internal GMP audit in MY plant, contract manufacturers, external laboratories and J&J affiliates on microbiological aspects and ensuring compliance to Kenvue requirements.
- Facilitates the development and training of lab team members.
- Ensures a strong pipeline of talent for leadership roles and critical positions.
- Partners with industry leaders, and sector/enterprise senior technical stakeholders, to develop and implement best practices and improvement opportunities.
- Ensure entire Quality Control Laboratory analyst are trained and qualified to perform laboratory task and testing effectively and efficiently.
- Manage the budget allocation for Quality Control Laboratory and ensure laboratory inventory is enough to avoid interruption in daily laboratory operation.
What We Are Looking For
- Bachelor's degree in a relevant field or equivalent experience
- Minimum 5 years of experience in quality control or related field, implementation of QMS in the lab and strong GLP background.
- Strong knowledge of industry standards and regulations, and experience developing and implementing quality control procedures.
- Excellent communication and negotiation skills
- Ability to lead and manage a team effectively
- Strong problem-solving and analytical skills, with the ability to identify and resolve issues quickly and effectively.
- Experience with lab equipment management, validation of equipment and test methods and testing procedures, and the ability to troubleshoot issues as needed.
- Excellent leadership and communication skills, with the ability to motivate and mentor team members.
- Highly organized and detail-oriented, with the ability to manage multiple projects simultaneously.
- Result-oriented and proactive mindset
- Entrepreneurial understanding to drive innovation and growth
- Superior presentation skills to effectively communicate with stakeholders
- Advanced skills and specialized software knowledge
- Competitive Benefit Package*
- Paid Company Holidays, Paid Vacation, Volunteer Time, & More!
- Learning & Development Opportunities
- Employee Resource Groups
- This list could vary based on location/region
- Note: Total Rewards at Kenvue include salary, bonus (if applicable) and benefits. Your Talent Access Partner will be able to share more about our total rewards offerings and the specific salary range for the relevant location(s) during the recruitment & hiring process.
If you are an individual with a disability, please check our Disability Assistance page for information on how to request an accommodation. Seniority level
- Seniority level Mid-Senior level
- Employment type Full-time
- Job function Quality Assurance
- Industries Personal Care Product Manufacturing
Referrals increase your chances of interviewing at Kenvue by 2x
Sign in to set job alerts for “Quality Assurance Manager” roles. Director - Tech Advisory (PwC Acceleration Center Kuala Lumpur)Kuala Lumpur, Federal Territory of Kuala Lumpur, Malaysia 1 month ago
Manager - Assurance (PwC Acceleration Center Kuala Lumpur)Kuala Lumpur, Federal Territory of Kuala Lumpur, Malaysia 1 week ago
Manager - Assurance (PwC Acceleration Center Kuala Lumpur)Kuala Lumpur, Federal Territory of Kuala Lumpur, Malaysia 5 months ago
Kuala Lumpur, Federal Territory of Kuala Lumpur, Malaysia 3 months ago
Federal Territory of Kuala Lumpur, Malaysia 1 week ago
Kuala Lumpur, Federal Territory of Kuala Lumpur, Malaysia 5 days ago
Supervisor, Audit T&E (Travel & Expenses)Petaling Jaya, Selangor, Malaysia 4 days ago
Senior Manager - Assurance (PwC Acceleration Center Kuala Lumpur)Kuala Lumpur, Federal Territory of Kuala Lumpur, Malaysia 5 months ago
Audit Manager (PwC Acceleration Center Kuala Lumpur)Federal Territory of Kuala Lumpur, Malaysia 1 week ago
Quality Assurance & Technical Senior ManagerKuala Lumpur, Federal Territory of Kuala Lumpur, Malaysia 4 weeks ago
Federal Territory of Kuala Lumpur, Malaysia 6 days ago
Kuala Lumpur, Federal Territory of Kuala Lumpur, Malaysia 3 weeks ago
Quality Assurance & Workforce Management ManagerKuala Lumpur, Federal Territory of Kuala Lumpur, Malaysia 1 week ago
Federal Territory of Kuala Lumpur, Malaysia 2 months ago
Senior Manager - Assurance (PwC Acceleration Center Kuala Lumpur)Kuala Lumpur, Federal Territory of Kuala Lumpur, Malaysia 1 week ago
Regional Quality Assurance and Control Manager - Data Centre DevelopmentsSeksyen 10, Federal Territory of Kuala Lumpur, Malaysia 1 month ago
Petaling Jaya, Selangor, Malaysia 1 month ago
Kuala Lumpur, Federal Territory of Kuala Lumpur, Malaysia 1 week ago
Kota Damansara, Selangor, Malaysia 3 weeks ago
WP. Kuala Lumpur, Federal Territory of Kuala Lumpur, Malaysia 1 week ago
Petaling Jaya, Selangor, Malaysia 4 days ago
Kuala Lumpur, Federal Territory of Kuala Lumpur, Malaysia 1 month ago
Federal Territory of Kuala Lumpur, Malaysia 1 week ago
Internal Auditor - Regional Audit Hub APACKuala Lumpur, Federal Territory of Kuala Lumpur, Malaysia 2 days ago
Senior Engineer - Quality Assurance/Quality Control 1Petaling Jaya, Selangor, Malaysia 4 months ago
Petaling Jaya, Selangor, Malaysia 6 days ago
Quality Assurance & Technical Senior ManagerKuala Lumpur, Federal Territory of Kuala Lumpur, Malaysia 1 month ago
(MANDARIN SPEAKERS) Regulatory Affairs ExecutiveWe’re unlocking community knowledge in a new way. Experts add insights directly into each article, started with the help of AI.
#J-18808-Ljbffr